CO2 reduction
Transportation of molten aluminium
Aluminium alloys for casting and die casting are usually cast into ingots and then re-melted by users for molding. However, the transportation of molten aluminium to users without casting it into ingots reduces the energy used for re-melting and significantly decreases CO2 emissions.
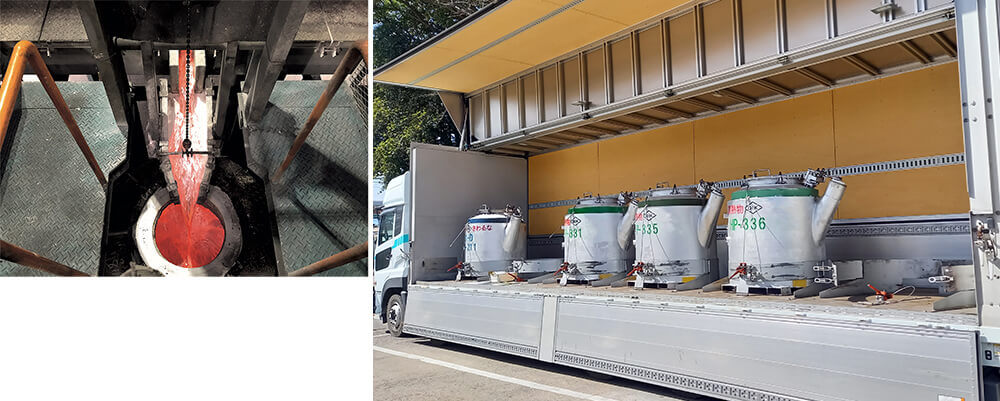
Introduction of exhaust heat recovery burners
In the transportation of molten aluminium, the aluminium is poured into pots and delivered to users in a molten state.
When it is poured into a pot, the pot is preheated with an LPG burner to prevent the temperature of the molten aluminium from decreasing. Ordinary gas burners emit exhaust gas into the air in the same way as gas stoves do at home.
By introducing exhaust heat recovery burners, which can effectively utilize the amount of heat in exhaust gas, consumption of LPG gas can be reduced by approximately 6%.
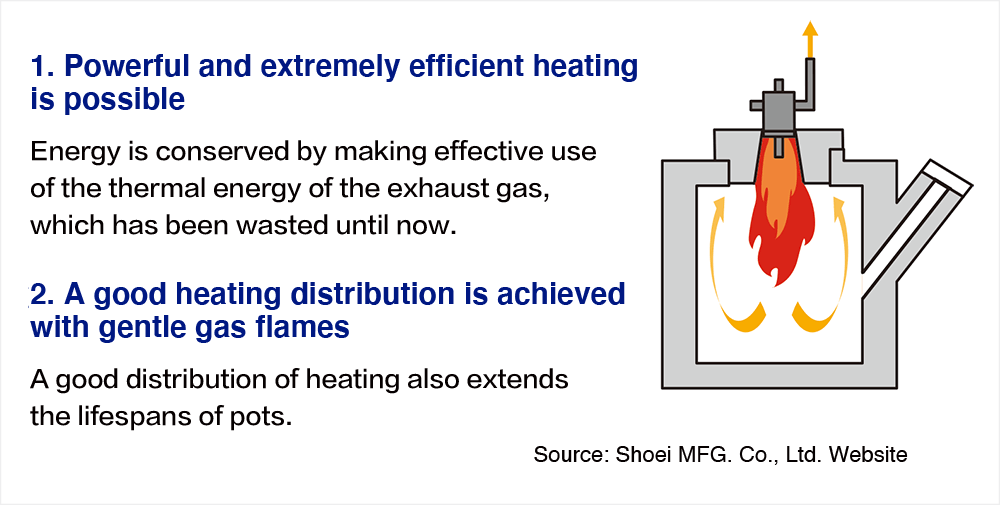
Reduction of compressor power consumption by looping high-pressure air distribution piping
As a measure to save energy, we are promoting the looping of compressor air piping.
High-pressure air supplied by a compressor is an important power source for the operation of production equipment in plants. Compressors use electricity to generate high-pressure air.
The shift to looped piping can reduce the difference in pressure between the end of the piping connected to the compressor and the other end of the piping in comparison with conventional one-way piping, which supplies high-pressure air through one channel. As a result, the pressure set at the compressor can be lowered, and this has the effect of lowering the power consumption of the compressor.
Installation of inverters for various motors
We have introduced inverter control for the motors of large dust collectors in our plants to enable the air volume for dust collection to be adjusted finely according to the operating conditions (smoke generation). This initiative eliminates the wasteful use of electricity and helps to reduce CO2 emissions.
Introduction of regenerative burners
A regenerative burner is a type of burner that uses a heat exchanger to make effective use of exhaust heat from a furnace. A heat reservoir is heated with the waste heat of the furnace, and combustion air is preliminarily heated by passing it through the heated heat reservoir. The introduction of regenerative burners can reduce the use of heavy oil by more than 30%.
Use of LED lighting
Manufacturing plants require a great deal of lighting. As an initiative to reduce the environmental impact, we replaced our lighting with LED lighting fixtures, which consume less electricity and help reduce CO2 emissions.
Energy conservation Working Group
Energy conservation Working Group meetings are held periodically in each plant as an initiative of the Technical Department.
By sharing the energy conservation activities being undertaken at each plant and information about them, we are implementing even more energy conservation activities.