DIK365
- Aluminium alloys
- Aluminium alloys for high pressure die casting
- Special alloys
- Automobiles and motorcycles
- Various on-vehicle parts
- Precision equipment
- Frames
Features
Widely used for structural parts in Europe, this alloy has high ductility and high corrosion resistance.
1
In terms of composition, it is an Al-Si-Mg-Mn alloy.
2
Physical properties
Table 2-1. Physical properties
Density g/cm3 |
Liquidus temperature ℃ |
Solidus temperature ℃ |
Thermal expansion coefficient ×10-6/℃ |
Specific heat J/(kg・K) |
Thermal conductivity* W/(m・℃) |
|
---|---|---|---|---|---|---|
DIK365 | – | 602 | 573 | – | 876 | 128 |
ADC12 | 2.68 | 582 | 515 | 21.0 | 911 | 125 |
*Thermal conductivity was measured with test pieces cut from a flat die casting sample (50 x 100 x 5 mm).
Table 2-2. Mechanical properties
(a) Hardness properties
Heat treatment conditions | Brinell hardness HBW |
Rockwell hardness HRB |
Micro Vickers hardness HV 0.5 |
---|---|---|---|
F | 69 | 32.4 | 79 |
T5(180℃×3h) |
73 | 41.8 | 87 |
・Sample: flat die casting sample
(b) Tensile properties
Element (wt. %) |
Heat treatment |
Tensile strength (MPa) |
Elongation (%) | 0.2% proof stress (MPa) | ||||||
---|---|---|---|---|---|---|---|---|---|---|
Cu | Si | Mg | Zn | Fe | Mn | Sr | ||||
0.01 | 10.03 | 0.43 | 0.01 | 0.12 | 0.56 | 0.0168 | F | 323 | 8.8 | 159 |
T5 | 361 | 6.1 | 258 | |||||||
T6 | 317 | 6.5 | 265 |
・Test pieces: ASTM tensile strength test pieces
・F: as cast
・T5: 180℃×3h
・T6: 510℃×3h→180℃×3h
3
Other features: Corrosion resistance
Table 3. Corrosion resistance test samples: component values
Sample name | Element (wt. %) | ||||||
---|---|---|---|---|---|---|---|
Cu | Si | Mg | Zn | Fe | Mn | Sr | |
ADC12 | 1.73 | 10.17 | 0.24 | 0.64 | 0.86 | 0.18 | – |
DIK365 | 0.01 | 10.03 | 0.43 | 0.01 | 0.12 | 0.56 | 0.0168 |
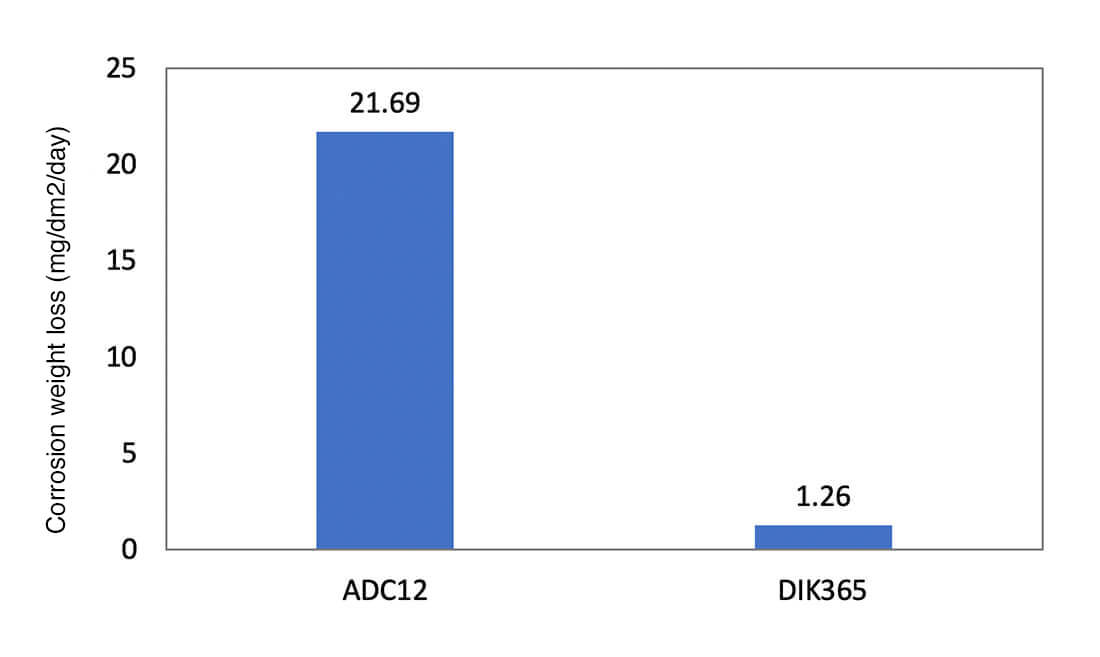
*Flat die casting sample (50 x 100 x 5 mm)
*Test period: 720 hr (n=3)
- Melting temperature: A temperature from 680 to 700°C is recommended, although it also depends on the casting design.
- Flux: Flux for ADC12 is acceptable.
- About the use of return materials
(1) When priority is given to mechanical properties
Return materials cannot be used because attenuation of Mg and Sr causes the mechanical properties to change. However, they can be used if an analysis of Mg and Sr indicates that the addition of return materials is possible.
(2) When priority is given to corrosion resistance
Return materials can be used. Use of return materials does cause attenuation of Mg and Sr, but it does not affect the corrosion resistance.
Remarks
Please note that the figures described in the above technical data are based on our measurements and are not guaranteed.